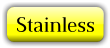
Invar 36, Invar 42, Kovar Alloys |
Sheet, Plate, Bar
Please
call 800-707-6061 or fax RFQs to 800-707-3439. We will get back to you ASAP.
Thanks.
* All Trademarks and/or Trade
names are the properties of their respective owners.
About Invar
Invar, also known as Invar 36, is a nickel steel
alloy with unique low rates of thermal expansion.
1) Invar 36
* Invar 36 Sheet, Plate Per Chem Mil-I-23011C CL
7, Boeing D-33028, ASTM-B-753, F-1684
Thickness: 0.015"~6.000" , Width:
10"~72", Length: 60"~144"
* Invar 36 Bar Per Mil-I-23011 CL 7, ASTM-B-752 Chem
Only, Chem Mil-S-16598B, ASTM-F1684
Diameter: 0.078"~6.000", Length: 144" Random Length
2) Invar 42
* Invar 42 Plate Per Chem Mil-I-23011 CL 5, Chem
ASTM-F-30, Chem ASTM-B-753
Thickness: 0.250"~4.000", Width: 18"~48",
Length: 12"~144"
About Kovar
Kovar alloy is a vacuum melted,
iron-nickel-cobalt, low expansion alloy whose chemical composition is
controlled within narrow limits to assure precise uniform thermal expansion
properties.
3) Kovar
* Kovar Sheet, Plate Per Mil-I-23011 CL 1,
ASTM-F-15, Thickness: 0.005"~1.000", Width: 12"~48", Length: 36"~120"
* Kovar Bar Per ASTM-F-15, Diameter: 0.500"~0.500", Length: 144"
Random Length
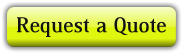
Invar 36 Specifications:
UNS K93600, UNS K93603
MIN |
35.0 |
- |
- |
- |
- |
- |
- |
- |
- |
- |
MAX |
37.0 |
Balance |
0.5 |
0.1 |
0.5 |
0.6 |
0.35 |
0.025 |
0.025 |
0.5 |
Features
- Low expansion rate up to 500 Degrees F
- Readily weldable
Applications
- Tooling and dies for composite forming
- Cryogenic components
- Laser components
Density:
0.293 lb/in3
Melting Point: 2605 Degrees
Electrical Conductivity: 69.3 Btu •
ft/ ft² • hr • Degrees F
Temperature, Degrees F |
-328 |
-148 |
212 |
302 |
392 |
482 |
572 |
662 |
752 |
842 |
932 |
Modulus of Elasticity, Dynamic psi x 106 |
0.8 |
0.7 |
0.8 |
1.1 |
1.4 |
1.9 |
3.1 |
4.0 |
4.7 |
5.2 |
5.6 |
* 70
Degrees F to indicated temperature.
Typical
Tensile Properties
Temperature, Degrees F |
68 |
212 |
392 |
572 |
752 |
932 |
1112 |
Ultimate Tensile Strength, ksi |
71 |
62 |
62 |
59 |
51 |
42 |
30 |
0.2% Yield Strength, ksi |
35 |
26 |
16 |
13 |
13 |
13 |
11 |
Elongation, % |
42 |
43 |
45 |
48 |
53 |
59 |
68 |
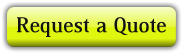
Invar 42 Specifications:
UNS K94100
Chemistry Data
Carbon |
|
0.05 max |
Iron |
|
Balance |
Manganese |
|
1 max |
Nickel |
|
|
Silicon |
|
|
|
General Information
Principal Design Features
This is an iron-nickel alloy with controlled
thermal expansion properties.
Applications
Used for glass-to-metal sealing of components that are enclosed in a glass
envelope, such as lamps and electron tubes.
Machinability
The alloy is readily machinable by conventional techniques.
Forming
Ductility and thus formability are very good.
Welding
The alloy may be welded by conventional methods.
Heat Treatment
An annealing heat treatment may be used. The alloy is not hardenable by heat
treatment.
Forging
Forging may be done at 2200 F. As is true of all the high nickel content
alloys care should be taken to avoid contamination from sulfur due to long
soaking time in a furnace atmosphere.
Cold Working
The alloy has good ductility and is readily cold worked.
Annealing
Anneal at 1450F (788C) followed by air cooling.
Hardening
Hardens due to cold working only.
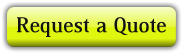
Physical Data
Density (lb / cu. in.) |
|
0.293 |
Specific Gravity |
|
8.12 |
Specific Heat (Btu/lb/Deg F - [32-212 Deg F]) |
|
0.12 |
Electrical Resistivity (microhm-cm (at 68 Deg F)) |
|
494 |
Melting Point (Deg F) |
|
2600 |
Mean Coeff Thermal Expansion |
|
0.8 |
Modulus of Elasticity Tension |
|
21.5 |
Kovar Specifications:
UNS K94610
General Properties
Symbol: |
Ni, Fe, Co alloy |
Weight Percent: |
29% Ni, 17% Co, 53% Fe, 1% trace |
Density: |
8.36 g/cm3 |
Melting Point: |
2642 Degrees F (1450 Degrees C) |
Thermal Conductivity: |
16.8 W/mk |
Electrical Resistivity: |
0.49 microhm-m |
Expansion Coefficient: |
5 ppm/ Degrees C |
Typical Analyses
Chemical Composition
Material / Purity: |
Kovar |
Mn |
0.30 |
Si |
0.10 |
Ni |
29.0 |
Co |
17.0 |
Fe |
Bal. |
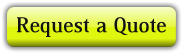
Workability
Forging
The principal precaution to observe in forging is to heat quickly and avoid
soaking in the furnace. Long soaking may result in a checked surface due to
absorption of sulfur from the furnace atmosphere and/or oxide penetration. A
forging temperature of 2000/2150 Degrees F is preferred.
Coolant
It is important to control heat build up, the major cause of warpage.
Tooling
One thing of prime importance is that all feathered or wire edges should be
removed from the tools. They should be kept in excellent condition by repeated
inspection.
Turning
If steel cutting tools are used, try a feed of approximately .010" to .012"
per revolution and a speed as high as 35/FPM could probably be attained. Some
of the angles on the cutting tools would be as follows:
-
End cutting edge
angle -Approximately 7 Degrees
-
Nose radius
-Approximately .005"
-
Side cutting edge
angle -Approximately 15 Degrees
-
Back rake
-Approximately 8 Degrees
-
Side rake
-Approximately 8 Degrees
When cutting off high speed tools are better
than carbide tools, and a feed of approximately .001" per revolution should be
used. The cutting tools should have a front clearance of about 7 Degrees and a
fairly big tip--larger than 25 Degrees would be helpful.
Drilling
When drilling a 3/16" diameter hole, a speed of about 40/FPM could possibly be
used, and the feed should be about .002" to .0025" per revolution, for a 1/2"
hole, approximately the same speed could be used with a feed of about .004" to
.005" per revolution. The drills should be as short as possible, and it is
desirable to make a thin web at the point by conventional methods. By
conventional methods, we mean do not notch or make a crank shaft grinding. It
is suggested that heavy web type drills with nitrided or electrolyzed surfaces
be used. The hole, of course, should be cleaned frequently in order to remove
the chips, which will gall, and also for cooling. The drill should be ground
to an included point angle of 118 Degrees to 120 Degrees
Reaming
Reaming speeds should be half the drill speed, but the feed should be about
three times the drill speed. It is suggested that the margin on the land
should be about .005" to .010", and that the chamfer should be .005" to .010"
and the chamfer angle about 30 Degrees. The tools should be as short as
possible, and have a slight face rake of about 5 Degrees to 8 Degrees.
Tapping
In tapping, a tap drill slightly larger than the standard drill recommended
for conventional threads should be used, because the metal will probably flow
into the cut. It is suggested that on automatic machines, a two or three
fluted tapping tool should be used. For taps below 3/16", the two fluted would
be best. Grind the face hook angle to 8° to 10°, and the tap should have a
.003" to .005" chamfered edge. If possible, if binding occurs in the hole in
tapping, the width of the land may be too great, and it is suggested that the
width of the heel be ground down. Again, it is suggested that nitrided or
electrolyzed tools be used. Speed should be about 20/FPM.
Please call 800-707-6061 or fax RFQs to 800-707-3439.
We
will get back to you ASAP. Thanks.